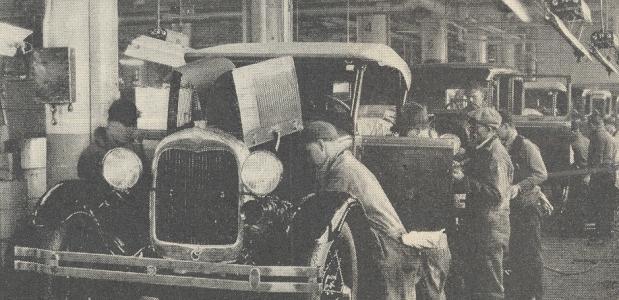
Van Ford tot computertaal: hoe automatisering ons werk veranderde
Grote bedrijven als Unilever en Shell zijn niet meer weg te denken uit onze maatschappij. Maar ooit was dat anders. Voor de industriële revolutie waren veruit de meeste bedrijven kleine organisaties, waar minder dan tien mensen werkten. Die verandering, van kleine naar hele grote bedrijven, heeft niet alleen de maatschappij, maar ook de manier waarop we werken veranderd.
Tijdens de Industriële Revolutie verdween de huisnijverheid. Eeuwenlang maakten veel ambachtslieden hun werkzaamheden in huis, of in een werkplaats die zich op hetzelfde erf als de woning bevond. In die werkplaats werkten vaak meer mensen. Dat waren de eigenaar en vaak de ‘meester’ en een aantal leerlingen en/of knechten. Hoewel er -uiteraard- vaak samengewerkt werd, werkte iedereen in zo’n werkplaats van begin tot eind aan een project. Hoewel een leerling niet altijd het hele product zelf maakte, was hij onder toeziend oog wel van begin tot eind bij de productie betrokken. Dat wil niet zeggen dat een leerling-meubelmaker een hele tafel in elkaar zette, maar tijdens het maken verrichtte hij hand-en-spandiensten voor zijn meester, waarna die de tafel volledig af kon maken. Door die kleine hand en spandiensten, die steeds groter werden, werd de leerling steeds meer bedreven in het vak, verbeterden zijn vaardigheden en leerde hij het ambacht van a- tot z, tot hij op een dag zelf in staat was om het hele proces te plannen en uit te voeren.
De eerste lopende-band processen
Met de opkomst van de industriële revolutie kwam daar verandering in. De werkplaatsen werden groter en groter en arbeiders in zo’n werkplaats hadden lang niet altijd meer de relatie die een leerling en een meester hadden. Doordat machines steeds vaker grote delen van het productieproces overnamen, hoefden veel werknemers niet meer het hele proces van a tot z te leren, maar slechts een klein stukje daarvan. Het schoolvoorbeeld van zo’n productieproces was de ‘lopende band’ die Henry Ford bedacht voor de productie van zijn T-Ford. In de fabriek van Ford bouwden de arbeiders niet een hele auto, maar deden maar één ding, de scharnieren aan de deuren bevestigen bijvoorbeeld. End an waren er ook nog eens verschillende afdelingen. Waar de ene afdeling van losse onderdelen een complete autodeur in elkaar zette, maakte een andere afdeling de motor, of de wielen. Pas op het laatst werden die verschillende onderdelen bij elkaar gebracht en in elkaar gezet – geassembleerd- tot een complete auto.
Door die manier van werken konden bedrijven veel sneller en veel meer produceren, maar zo’n lopende band, of assemblagelijn, zet je niet zomaar in elkaar. Het ontwerp van de auto moet er geschikt voor zijn, want al die losse onderdeeltjes moesten natuurlijk wel in exact de juiste volgorde in elkaar gepuzzeld worden. En dan moesten die werkzaamheden ook qua tijd op elkaar afgestemd worden. De lopende band draaide onverbiddelijk door en arbeiders moesten hun werk wel afhebben voordat het onderdeel waar ze aan werkten was doorgeschoven naar hun collega die de volgende handeling verrichte.
Workflow aan de lopende band
Dat ging nog wel eens mis. Arbeiders die te langzaam werkten probeerden met de onderdelen mee te lopen, waardoor ze op elkaar botsten, of ze kwamen er simpelweg niet aan toe, waardoor auto’s complete onderdelen misten. Henry Ford was op den duur niet meer de slimme ingenieur die een goede auto ontwierp, maar een manager die druk bezig was om de workflow in zijn fabrieken zo optimaal mogelijk te ontwikkelen. Daardoor organiseerde hij dat er precies op tijd een complete autodeur de half in elkaar gezette auto werd afgeleverd, maar vertellen hoe je een handgreep op een deur schroefde, dat deed hij niet. Net als de controle of die handgreep er ook écht zat en of die wel goed vast zat. En ook de verkoop van de auto’s werd door anderen gedaan. En om te kijken of de workflow ook écht optimaal was, sprak Ford niet zozeer met de mensen die direct aan de lopende band stonden, maar afdelingshoofden. De ‘tussen-managers’, als het ware. En eigenlijk deed Ford daarmee aan een soort workflow management avant la lettre.
Steeds complexer
De ontwikkeling die Ford had ingezet, was niet meer te stoppen. Doordat de techniek verbeterde, waren fabrieken in staat om steeds complexere producten af te leveren. Maar die ingewikkelde apparaten vergden ook een steeds ingewikkelder productieproces. Het ontwikkelen van de ideale workflow voor het bouwen van een T-Ford kostte Ford jaren en tegenwoordig zijn er heel wat bedrijven waarbij het proces van ontwerp tot product nog veel ingewikkelder is geworden. Al was het maar omdat sommige producten alleen op papier bestaan. Denk maar aan allerlei verschillende soorten verzekeringen. Ook bij verzekeraars werken vaak verschillende afdelingen aan één eindproduct. De ene afdeling doet het contact met de verzekerden, de andere regelt dat de juiste vergoeding naar de juiste rekening wordt overgemaakt en weer een ander regelt dat dat op het juiste moment gebeurt. Maar waar je bij een T-Ford vaak kon zien of de assemblage goed liep en of er niet bijvoorbeeld een handgreep aan een deur miste, is dat bij zulke ingewikkelde producten als verzekeringen een stuk minder eenvoudig.
Van lopende band naar informatiemanagement
Vandaag de dag wordt het lopende band principe dus nog steeds gebruikt. Alleen wordt het nu toegepast op informatie die door de bedrijfsprocessen stroomt. Met deze informatie worden beslissingen gemaakt of nieuwe activiteiten opgestart. En ook dat moet vlekkeloos. De bekende slogan “Smart Input Smart output” zorgt dat informatie overal op het juiste moment aanwezig is. Door ook gebruik te maken van automatische controles op de informatie , de techniek staat voor niets, wordt ook geborgd dat de informatie altijd van goede kwaliteit is. Meneer Ford heeft waarschijnlijk nooit gedacht dat zijn gedachtengoed nog steeds actueel is!